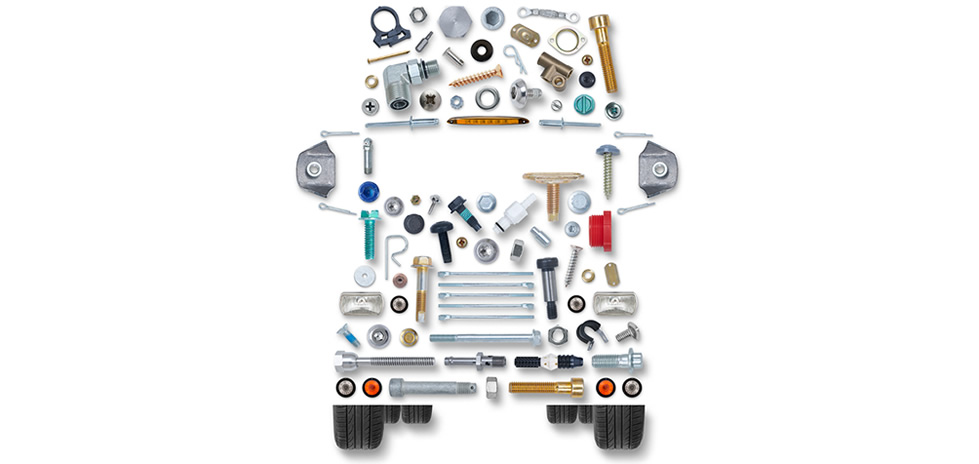
A global truck manufacturer partners with Optimas to standardize components for common production platforms, generating significant cost savings over the lifetime of the products.
Real Results, Real Impact
$5.9M
Lifetime Cost Savings
275
Parts Eliminated
50%
Higher Clamp Load
Situation
A global truck manufacturer with two leading brands used separate bills of material for discrete fastener parts causing unnecessary part proliferation, complexity and cost.
Solution
Optimas engineers collaborated with the manufacturer to standardize components from initial phase through development, testing and production. Being involved throughout the program allowed Optimas experts to rationalize component policy early, which minimized costs and delivered time efficiencies.
To generate savings and simplify parts, Optimas identified an existing joint that featured an expensive and archaic, cadmium plated, nylon locknut and mixed plating processes for each product platform. Optimas redesigned the joint to include a lighter and more cost-effective, metal locknut with a special topcoat and a common plating for all three components.
The solution offered significant cost savings and boosted product performance with a more repeatable torque tension relationship, improved paint adhesion, no temperature restrictions and elevated corrosion resistance from the nylon alternative. The lighter locknut also permitted a shorter bolt allowance, which improves fuel economy – a major concern for commercial trucks. In addition, the joint installation required no change to existing tooling and its introduction eliminated 275 part numbers.
Results
Optimas fastening experts’ standardized joint design and plating for both product platforms generated significant savings and performance improvements:
- Offered a $5.9 million lifetime cost savings and eliminated redundant inventory
- Increased clamp load by 50% to 22,500 lbs and normalized corrosion protection at 240 hours of salt spray
- Eliminated 275 parts between brands removing costs, risk and complexity
- Reduced weight by 10% from replacing the original nylon parts with metal parts
- Improved assembly processes with less torque while maintaining existing tooling
“Over a full production run, redesigning and standardizing this joint offered both brands significant cost savings while improving product performance for their customers.”
Steve Adkins
North American Director of Engineering,
Optimas
DOWNLOAD Case Study